1嵌件注塑的观点
塑料内部镶嵌有金属、玻璃、木材、纤维、纸张、橡胶或已成型的塑胶件等称为嵌件,最常见的嵌件为金属。
嵌件注塑(Insert Molding)是一种将嵌件预先固定在注塑模具中适当的位置,然后再注入塑料成型,开模后嵌件被冷却固化的塑料包紧埋在塑料内得到带有如螺纹、电极等嵌件的制品的工艺。
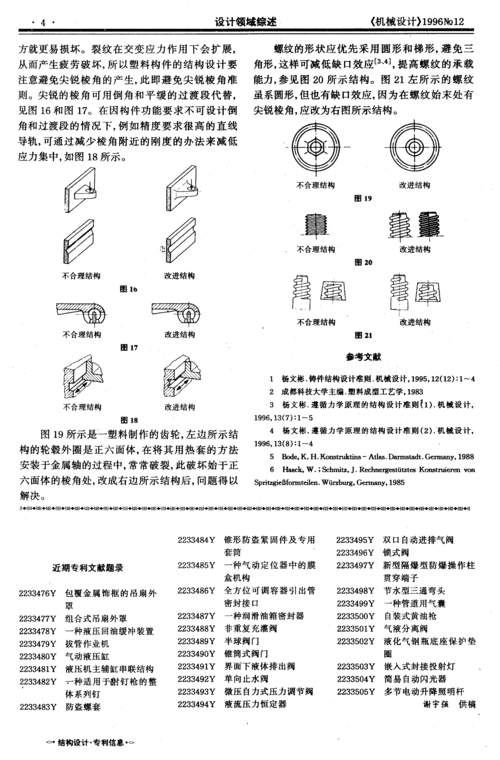
嵌件注塑时嵌件在模具中的放置有两种方法:
1)人工放置;这会大幅增加注塑成型周期,适用于小批量生产或者繁芜构造的产品;
2)自动化放置;这是大批量生产的更佳选择,有利于减少人工失落误、提高效率、缩短注塑成型周期和提高产品的可靠性。
2嵌件注塑的优缺陷
2.1 嵌件注塑的优点
1)塑料的易成型性、弹性性与金属的刚性、強度及耐热性的相互组合补充可结实地制成繁芜风雅的金属塑料一体化产品;减小产品的尺寸和重量;
2)利用塑料的绝缘性和金属的导电性的组合,制成的成型品能知足电气产品的基本性能;还可以知足某些分外哀求,如导磁、耐磨和紧固等;
3)塑估中加入金属嵌件,可以提高塑胶件的强度;
4)嵌件注塑增加了产品设计灵巧性,给塑料和金属及其它零件的结合供应了新的可能;
5)避免热熔、焊接和铆接等二次工序,有机会缩短装置韶光和本钱;
6)嵌件不仅限于金属,也有布、纸、电线、塑料、玻璃、木材、线圈类、电气零件和塑胶件等多种;
7)对付刚性成型品、橡胶密封垫板上的波折弹性成型品,通过基体上注塑成型制成一体化产品后,可省去排列密封圏的繁芜作业,使得后工序的自动化组合更随意马虎;
8)由于是熔融塑料与金属嵌件等结合,与压入成型法等比较较,金属嵌件间隙可以设计得更狭窄,产品可靠性更高;更随意马虎通过振动等测试;
9)选择适当的塑料和成型条件,即是对付易変形破损的产品(如玻璃、线圈类、电气零件等),通过塑料也可密封固定;
10)选择适当的模具布局,嵌件品也可完备封入塑料内。
11)立式注塑机与机器手、嵌件品整列装置等的组合,嵌件成型工程大都可实现自动化生产。
2.2 嵌件注塑的缺陷
1)嵌件的放置每每使模具构造繁芜化,注塑成型周期延长,制造本钱增加,加大自动化生产难度;
2)嵌件与塑料的热膨胀系数不一致,随意马虎使得终极的产品产生内应力,而造成产品分裂;这一点,在螺母嵌件的注塑成型中显得特殊明显;
3)或者由于嵌件与塑料的热膨胀系数不一致,造成产品发生变形;
4)嵌件(特殊是螺母嵌件)每每须要预热或干燥处理等,以减小内应力;
5)嵌件必须在模具中很好的固定,否则很随意马虎在溶料的冲击下发生移位或变形;
6)嵌件注塑一旦产生不良品例如注塑不良、嵌件遗漏、位置不良等,会造玉成部产品报废,代价巨大;
7)嵌件注塑不利于产品回收与报废。
3嵌件注塑的运用
嵌件注塑广泛运用汽车、医疗、电子产品和连接器等各行业。
4嵌件注塑的设计指南
在设计嵌件注塑时,必须充分考虑到嵌件注塑的工艺特点,进行DFM的设计;
嵌件注塑的设计指南包括:
1)嵌件材料的选择。铜、铝、钢、硬质异种塑件、陶瓷、玻璃和塑料等都可作为嵌件材料,个中,黄铜不生锈、耐堕落、易加工且价格适中,是嵌件的常用材料。
2)嵌件形状。尽可能采取圆形或轴对称形,不许可存在尖角或锐角,以利均匀紧缩和防止产生局部应力,乃至应力集中征象;
3)嵌件本身须要考虑自身DFM。金属嵌件采取切削或冲压加工而成,因此嵌件形状必须有良好的加工工艺性。
▲嵌件本身DFM设计
4)为便于在模具中放置与定位,嵌件的外伸部分(即安顿在模具中的部分)应设计成圆柱形,由于模具加工圆孔最随意马虎;
▲嵌件外伸部分的设计
5)嵌件应有密封凸台等构造,以防止注塑成型时防止溢料;
▲嵌件凸台的设计
6)为避免塑料底部过薄涌现波纹形缩痕而影响外不雅观及强度,应取嵌件底面距塑料壁面的最小间隔T>D/6;
▲嵌件与底部的间隔
当间隔过小时,可以采取下图所示的设计;
▲担保壁厚均匀
7)嵌件与产品侧壁的间距不能过小,以担保模具有一定的强度;
▲嵌件与侧壁的间隔
8)凸台中设置嵌件时,为担保嵌件结合稳定以及塑料基体的强度,嵌件应伸人到凸台的底部(需担保最小底厚),嵌件头部作成圆角;
▲凸台中的嵌件
9)小型圆柱形嵌件可用中间开槽或表面菱形滚花构造植于塑料基体之中,滚花槽深1~2mm;
▲小型圆柱形嵌件的固定
10)板、片状嵌件可用孔窗固定法固定,但薄形嵌件(厚度小于0.5mm)宜用切口或打弯的方法固定;
▲板、片状嵌件的固定
11)杆形嵌件可用将头部打扁、冲缺、压弯、劈叉等形式固定,也可用将圆杆的中间部分压扁的方法固定;
▲杆形嵌件的固定(头部变形)
▲管形嵌件的固定(中间变形)
12)管形冲压嵌件,可在冲压时加工出膨凸部分,用以增强紧固力;
▲管形冲压件的固定(中间变形)
13)在连接器中,端子嵌件在塑估中固定的稳定性是每一位产品设计工程师优先要考虑的问题,常用的方法有以下几种,可极大的增强端子在塑估中的稳定性;
塑估中端子打孔;塑估中端子异形;塑估中端子折弯;塑估中端子增加粗糙度,凹凸点;增加塑料壁厚。▲端子嵌件打孔、异形、折弯
5螺母嵌件的设计指南
螺母嵌件是最常见的嵌件之一,螺母嵌件及对应的塑胶件支柱必须精确的设计,否则会涌现拔着力不足、支柱分裂等质量问题。
5.1 螺母的三种埋入办法
把螺母埋入塑胶件中有三种办法:
1)热熔螺母
热熔埋置是最常见、最常日的埋入办法,一样平常以热熔机及手工电烙铁埋钉;
2)嵌件注塑螺母
注塑成型埋置一样平常对螺母支柱的孔径哀求很严格,孔径管控在0.05mm以内,由于产品以ModingPin固定后放置于射出成型模具中,螺母孔径要以注塑成型机的PIN针的大小来管控;
3)超声波螺母
超声波埋置是一种通过超声振动,使螺母与工件表面及内在分子间的磨擦而使传处到接口的温度升高,当温度达到此工件自身的软化温度时,将螺母埋植于胶件中,当震撼停滞,工件同时在一定的压力下冷却定形。
三种办法各有优缺陷,本文谈论的是嵌件注塑螺母。
5.2 嵌件螺母的形状构造
5.3 嵌件螺母的规格示例
5.4 塑胶件支柱设计与螺母选择
1)螺母基本尺寸和塑胶件支柱基本尺寸
d尺寸为螺母底座,也称导向定位部分,在埋入前与塑胶C部分合营,因此螺母底端d部分要比塑胶件支柱内孔径C尺寸小,以方便定位;D尺寸为螺母外径,它与塑胶件支柱内孔径C尺寸相配,一样平常手机螺母塑胶内孔径比螺母外径小约0.25-0.3mm;L尺寸为螺母长度,它与塑胶件支柱孔深度Y尺寸合营,一样平常塑胶孔深比螺母高(长)度大0.5-1.0mm的深度用于储胶;W为塑胶孔壁厚,一样平常塑胶件支柱孔肉厚为0.8-1.0mm以上,螺母尺寸规格越大,肉厚越大。(见下表参数)5.5 常见问题及办理方案
1)精确的塑胶件支柱孔尺寸至关主要。塑胶件支柱孔太大,螺母埋入塑胶后吃不到胶,会产生扭拉力不敷征象;塑胶件支柱孔太小,会产生溢胶或者分裂征象;
2)如螺母尺寸与塑胶尺寸都没有问题,还有非常征象发生,那常日会考虑通过一些优化设计来改进;
由于塑胶件支柱深度较浅,如选择双斜纹的螺母,在螺母各尺寸比例调配下,特殊是压花上,压花段差较短,这样的螺母埋入塑胶后,压花吃胶面的塑胶太少,会产生扭拉力不敷征象,以是一样平常建议,将塑胶件支柱孔深设在2.5mm以上,螺母尺寸长度一样平常建议做2.0mm以上。改进方案:类似这种情形,在未便利改模情形下,可建议将螺母花形改为单斜BS1,如右图所示,这样将压花段差加大,压花吃胶面的塑胶增大,从而增加扭拉力。
3)塑胶件支柱孔溢胶或者分裂;
由于选择左图样式螺母,在埋入塑胶后,A1、A2处膨胀,B处却急剧紧缩,造成塑胶排挤困难,螺母高下端随意马虎产生溢胶征象,严重影响了产品外不雅观;
改进方案:以“C”部分为导向定位,使螺母能稳妥地放入塑胶孔位中,提高了效率和良品率,由于加了C端导向部分,A2排挤一定的胶料后,也预留了足够的胶料给A1部分,同时因A1、A2部分是呈90°交角为45°的斜纹,并可交角形成高强度的节点,阻抗圆周上的扭动力,使扭拉力大大的增加。
6资料***
嵌件注塑是相比拟较繁芜的工艺,个中的水还比较深,以上仅仅是做一个大略性的先容;工程师在设计干系详细产品之前,建议去搜索、阅读更多的资料。
以下是我搜集的与嵌件注塑有关的资料,大家如果有兴趣,请私信我。
—END—
1. 免责声明:部分图片和资料来源于网络,仅供学习用,侵权删。
2. 原创作品,欢迎转载,抄袭必究。如需转载,请联系作者,转载哀求不能修正内容和保留文末作者及公众年夜众号信息。
推举阅读:
降本圣经:《降本设计之道》助工程师升职加薪,助企业降本!
关于作者:
钟元,2020年3月出版《面向本钱的产品设计:降本设计之道》
2011年出版书本《面向制造和装置的产品设计指南》
欢迎关注“降本设计”头条号,获取更多原创降本设计知识和理念!
头条号聚焦降本设计知识分享和方案供应,助工程师技能提高和职场发展,助企业降本和利润提升。