而倒装芯片技能被广泛运用于前辈封装技能领域,可以有效办理芯片与基板之间因应力不匹配产生的可靠性问题。底部添补工艺通过在芯片和基板的间隙添补有机胶,使得应力可以被重新分配,进而起到保护焊点的浸染,提升封装可靠性。随着芯片不断向轻薄化方向发展,芯片尺寸的缩减和构造的风雅化导致对添补材料的性能及封装可靠性的哀求不断提高,底部添补工艺面临着更大的寻衅。材料设计、工艺优化等方法是应对潜在寻衅的有效办法。
随着芯片越来越趋于小型化和轻薄化,封装技能不断朝着高密度集成的方向发展,传统的引线键合难以知足前辈封装的需求和发展趋势,因此倒装芯片技能应运而生。倒装芯片技能具有旗子暗记传输路径短、散热性能好、电感电容低等上风,可实现高密度、小尺寸的封装,在实际运用中有着广阔的前景。
倒装芯片技能是通过凸块实现芯片与基板的直接键合,由于芯片与基板的热膨胀系数(CTE)不匹配会产生应力,可能导致焊接失落效乃至产生裂纹,从而影响产品可靠性。目前行业内普遍采取底部添补工艺来办理应力问题。通过利用环氧树脂添补芯片与基板之间的间隙,可以有效地分散芯片所受的应力。同时,这种方法还能隔离焊点与外界环境的直接打仗,从而保护焊点并提升芯片的可靠性。为了优化环氧树脂的性能,常日会在个中添加二氧化硅等材料,使其表现出高模量、低 CTE、低吸湿性和良好的黏附性等特点。
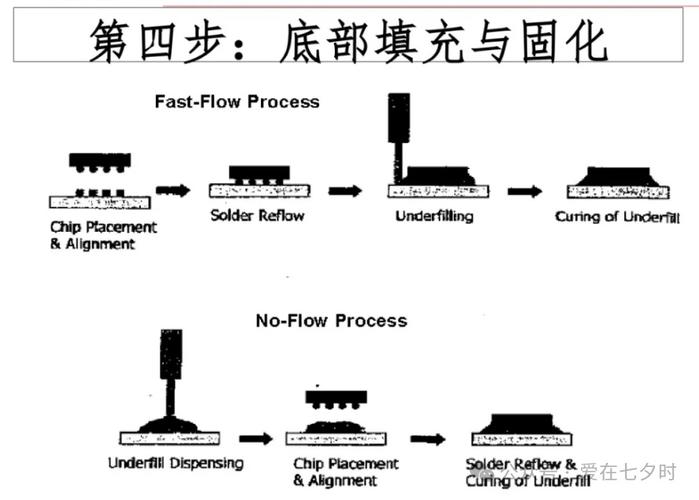
目前主流的底部添补工艺有流动式、非流动式、模压式和晶圆级等。随着芯片的集成化程度越来越高,凸块间距越来越小,倒装芯片的间隙也不断缩小,无铅焊料的大范围利用、底部添补工艺效率、材料选择和封装高可靠性对底部添补工艺提出了新的哀求。本文紧张先容底部添补工艺的过程和改进方法,以及其研究进展和面临的寻衅。
大略来说,底部添补工艺便是将环氧树脂胶水点涂在倒装晶片边缘,通过“毛细管效应”,胶水被吸往元件的对侧完成底 部充填过程,然后在加热的情形下胶水固化。为了加快胶水添补的速率,每每还须要对基板进行预热。利用“毛细管效应”进行底部添补的工艺分为以下几个步骤:
·基板预热;
·分配填料(点胶);
·毛细流动;
·加热使填料固化。
为什么倒装晶片焊接完后都须要进行底部添补呢?我们来看焊接完成之后组件中材料,个中有电路板、元器件 和电路板材料为有机材料,如环氧树脂玻璃纤维加强材料、铜焊盘及线路、焊盘上其他金属和阻焊膜,而元件基 材是硅,还有金属焊球。所有这些材料热膨胀系数都不一致,轻微的热变形可能会造成组件内应力集中的征象, 由于倒装晶片组件的焊点非常小,很随意马虎在此过程中分裂。之以是须要底部添补是由于倒装晶片组件:
①材料之间热膨胀系数不匹配;
②波折变形可能造成失落效;
③跌落/冲击/机器振动造成失落效;
④静态负荷,如散热片事情产生的热量导致失落效;
⑤须要提高热循环寿命。
底部添补足为基于毛细流动的底部添补和预先施加胶水的非流动性底部添补工艺。下图中,便是因未进行底部添补,SnPb焊点涌现疲倦裂纹
一、流动式底部添补工艺
流动式底部添补工艺(CUF)利用树脂材料通过毛细浸染力流入芯片和基板之间的间隙。该工艺涌现较早,因此被认为是传统的底部添补工艺,其工艺流程如下图所示。在基板上涂覆一层助焊剂,把芯片翻转颠倒在基板上,通过加热完成键合,随后洗濯掉残余的助焊剂。通过动力系统(如点胶机)把适量底部添补胶沿着芯片边缘注入基板和芯片之间的空隙,底部添补胶在毛细力的浸染下向芯片中央流动,逐渐填满芯片和基板之间的空隙。完成添补后进入加热固化环节,将芯片、底部添补胶和基板黏接成一个整体。在此过程中,残留的助焊剂会影响添补材料的性能,导致固化后形成空洞,影响产品的可靠性。全体添补过程较为缓慢。一些研究者对不同点胶办法(单面点胶、L形点胶、U 形点胶)进行仿真实验,结果表明,不同的点胶办法对底部添补胶的流动和添补韶光有主要影响。因此,在履行底部添补前,需根据不同的封装设计哀求,选择得当的点胶办法和添补材料,打算出所需底部添补胶的质量和体积,估算添补韶光,提高底部添补的效率和可靠性。
范例的流动式底部添补胶是由液体有机树脂黏结剂和无机填料组成的稠浊物。常日利用环氧树脂稠浊物作为有机树脂黏结剂。除了环氧树脂外,固化过程中常常利用固化剂以形成交联结构。加入催化剂可以延长利用韶光和实现快速固化。常日在底部添补胶中加入 μm 级的二氧化硅作为无机填料,以改进固化后的材料性能,如降落 CTE、提高模量和降落吸湿性等,进而提高封装可靠性。NG 等深入研究了在底部添补胶中添加 nm 级二氧化硅的浸染,提出添加适当比例的 nm 级二氧化硅可以提高添补效率和可靠性。此外,还可以在底部添补胶中添加黏合促进剂、增韧剂和分散剂,添加剂有助于树脂的稠浊,可以增强固化后底部添补胶的性能。
底部添补物是一种液态封装物,常日是大量添补 SiO2 的环氧树脂,用于倒装芯片互连后的芯片和基底之间。固化后,硬化的底部添补物具有高模量、与焊点相匹配的低 CTE 、低吸湿性以及与芯片和基板的良好粘合性。焊点上的热应力在芯片、底部添补物、基板和所有焊点之间重新分配,而不是集中在外围焊点上。实践证明,运用底部添补可将最主要的焊点应变水平降落到未封装焊点应变的 0.10-0.25。因此,底部添补可将焊点疲倦寿命提高 10 至 100 倍。此外,它还能保护焊点免受环境的侵蚀。底部添补是将倒装芯片技能的运用从陶瓷基板扩展到有机基板,从高端产品扩展到本钱敏感型产品的一个切实可行的办理方案。
倒装芯片技能的进步推动了底部添补工艺和底部添补材料的发展。上图展示了采取底部添补工艺的倒装芯片的工艺步骤。芯片组装前后须要分别进行助焊剂点胶和洗濯步骤。芯片组装到基板上后,未添补材料被分配并拖入芯片与基板之间的缝隙中。
添补速度过慢一贯是流动式底部添补工艺的瓶颈之一,尤其是对付细间距、大尺寸、小空隙的芯片,添补韶光较长,还存在添补不完备和涌现空洞的风险。胡志勇采取加热基板的办法以降落底部添补胶的黏附,从而增大其流动性,缩短添补韶光;HO 等总结了影响空洞形成的成分,提出减少残留的助焊剂以及利用与助焊剂相兼容的底部添补胶,可以有效减少空洞;陈志健等通过优化固化工艺,确认三段式固化程序有助于肃清微气孔残留;WANG 等利用超声波赞助技能以改进工艺,研究超声驱动机理,创造超声波震撼有利于提高底部添补胶的流速;LIN 等通过优化凸块设计,创造采取合理的凸块形状和间距不仅可以缩短添补韶光,还能减少空洞的发生。流动式底部添补工艺操作大略,与各种添补胶和封装设计有较好的兼容性,虽然存在添补不完备和发生空洞的风险,在实际运用中仍被广泛采取。
二、非流动式底部添补工艺
非流动式底部添补工艺是在倒装芯片与基板键合提高行底部添补处理的工艺,其工艺流程如下图所示。首先将底部添补胶涂满基板,然后进行芯片倒装,在回流键合过程中完成底部添补胶的固化,直接省去了涂助焊剂、洗濯助焊剂和底部添补胶毛细流动等步骤,提高了添补效率。
非流动式底部添补胶不仅具有传统工艺所需的材料特性,还可以知足分外的哀求。由于省去了涂助焊剂的步骤,以是非流动式底部添补胶必须具备足够的助焊功能,SUNG 等研发了 1 种非流动助焊剂底部添补胶,可以有效去除焊料凸块和金属焊盘表面的氧化物,保持焊料的润湿性以及良好的焊接效果。底部添补胶还须要具有永劫光缓慢固化的特性,以确保在固化之前完成焊点键合。由于固化的底部添补胶会阻挡熔化的凸块与焊盘的结合,导致焊接不良,尤其是在利用高熔点无铅焊料时,须要添加得当的催化剂。ZHANG 等通过研究底部添补胶的固化行为,添加助溶剂(如金属螯合物)以调度不同环氧树脂的固化韶光,提高回流焊的良率。
在非流动式底部添补工艺中,在焊接凸块之间或者焊接凸块内部、底部创造空洞是很常见的,这是影响器件良率和可靠性的关键问题之一。通过剖析工艺条件、材料特性以及焊接凸块和底部添补胶之间的化 学 反 应 , 研 究 影 响 空 洞 形 成 的 多 种 因 素 。NASHRUDIN 等采取数值仿照与实验相结合的方法,提出在工艺过程中不同位置的速率和压力分布不一致可能是导致空洞形成的缘故原由。LEE 等在研究过程中创造焊料润湿性、焊料与底部添补胶之间的化学反应是导致空洞形成的主要成分。HURLEY 等通过建模研究焊料润湿性和空洞之间的关系,提出在焊料回流和底部添补胶固化过程中,挥发性气体的开释也是造成空洞的缘故原由之一。因此,选择得当的材料和工艺参数可以最大限度地减少非流动式底部添补工艺中的空洞。然而,由于工艺窗口常日比较窄,因此办理空洞问题是非流动式底部添补工艺的关键。
对付采取非流动式底部添补工艺封装的芯片,由于 CTE 不匹配引起 PCB 附近的焊料发生断裂是 1 种常见的失落效模式。KATSURAYAMA 等制备了 36 种具有不同热机器性能的底部添补胶,结果表明,具有高模量的底部添补胶有利于降落凸块内部积累的应变,具有低 CTE 的底部添补胶可以减少芯片封装后的翘曲。常用的改进方法是向环氧树脂中添加其他材料,使其具备低 CTE 和高模量。增韧剂可以起到提高底部添补胶韧性的浸染。同样,利用二氧化硅可以降落底部添补胶的 CTE,提高封装的可靠性。但二氧化硅的存在会影响焊接过程,因此须要将其和热压回流焊技能共同利用。LI 等利用带有官能团的硅烷偶联剂对二氧化硅颗粒进行了表面改性处理。将经由改性的 nm 级二氧化硅与热固性树脂稠浊,形成均匀分散的无团圆颗粒,利用这种材料同样可以得到较高的可靠性。由于 nm 级二氧化硅具有较大的比表面积,随意马虎形成团圆物,影响底部添补胶的性能,因此对其表面改性尤为主要。
利用非流动式底部添补工艺可以简化操作步骤,提高生产效率。然而热压回流焊技能和二氧化硅的利用并没有降落生产本钱。为理解决在工艺和热循环过程中涌现的焊点疲倦、芯片分裂等可靠性问题,须要研究者投入更多的精力开拓材料和工艺。
三、模压式底部添补工艺
传统的倒装芯片封装工艺是先利用流动式底部添补工艺封装,然后再对全体芯片进行包覆成型。虽然材料和工艺研究一贯在进步,但底部添补工艺依然是全体封装流程中耗时较长的工艺之一。为了优化封装流程,使其在降落本钱的同时又不影响可靠性,模压式底部添补工艺应运而生,该工艺可以将流动式底部添补工艺和包覆成型工艺相结合,模压填料不仅可以添补芯片和基板之间的间隙,还可以包覆全体芯片。模压式底部添补工艺的上风在于将底部添补工艺与塑封工艺合并为一体,从而缩短工艺韶光。
模压式底部添补工艺采取的是改性的环氧树脂模塑料(EMC)。EMC 在芯片塑封领域已经被运用多年,其具有卓越的可靠性。与传统的底部添补胶比较,可以通过向改性的 EMC 中添加质量分数为 80%的二氧化硅,以实现与焊点、基底紧密匹配的低 CTE 特性。
模压式底部添补工艺流程如下图所示,该工艺类似于加压的流动式底部添补工艺,首先在焊接好芯片的基板上放置模具,向模具中注入 EMC,然后加热固化底部添补胶。利用 EMC 不仅可以添补芯片和基板之间的间隙,还可以完玉成部组件的塑封。在此过程中,芯片的几何形状对底部添补胶流动产生较大的阻力,尤其是在添补间隙和凸块间距较小的情形下,随意马虎导致空气残留征象,因此模具设计尤为主要。模具设计一样平常采取排气设计,也可以利用真空赞助技能来防止空气滞留。SAITO 等通过选择含有眇小粒度添加料的添补胶,并提出了真空注塑技能和可移动排气阀技能,成功实现了间隙<8 μm、间距<15 μm 的可靠模压式底部添补工艺。
与流动式底部添补工艺比较,模压式底部添补工艺具有独特的上风。在流动式底部添补工艺中,利用毛细管式点胶在芯片四边形成圆角。底部添补圆角在点胶侧的宽度最大。因此,须要担保芯片边缘与封装边缘之间、2个芯片之间或 1 个芯片与临近无源元件之间的间隙最小。而模压式底部添补工艺不须要圆角,使得芯片之间的间隔更近,封装尺寸更小,封装或基板的本钱更低。此外,由于电容器和芯片上凸块之间的电感路径较短,电性能也将得到改进。YEN 等通过仿真打算、大量实验以及剖析量产数据,提出封装尺寸的缩小可节约 20%~25%的本钱,而采取多芯片堆叠技能可以节省更多本钱。但模压式底部添补工艺的适用范围依然较窄,在大尺寸芯片、细间距凸块和三维封装中紧张利用的依然是流动式底部添补工艺。
四、晶圆级底部添补工艺
为了能够与表面贴装技能(SMT)兼容,业界提出了 1 种改进的非流动式底部添补工艺———晶圆级底部添补工艺(WLUF),其工艺流程如下图所示。通过印刷或层压等工艺将底部添补胶涂覆在有凸块或者没有凸块的晶圆上。对付没有凸块的晶圆,底部添补胶可以作为掩模,不才一环节中被用于制备凸块。将晶圆切割成单个芯片,并利用 SMT 设备把单个芯片放置在基板上进行组装。该技能因具有本钱低、可靠性高的优点而备受关注,利用该技能不须要对晶圆后端工艺进行重大改变。
底部添补胶的选择、添补层的制备工艺、液体添补胶的半固化工艺、半固化后的划片和存储以及后续的焊料润湿等问题都是影响晶圆级底部添补工艺的关键成分。添补层须要均匀同等,一样平常采取旋涂、印刷等工艺实现。液态添补胶的半固化工艺涉及材料的部分固化和溶剂挥发。为了方便划片和储存,半固化的材料须要具有足够的稳定性和机器性能,在回流过程中还须要具有熔化和回流的能力,以便于凸块和焊盘的充分润湿并形成焊点,因此掌握固化过程至关主要。通过真空层压工艺将薄膜型的底部添补胶涂覆在晶圆上,然后直接切割晶圆。与旋涂工艺比较,由于薄膜型工艺无需进行半固化,因此操作更加简便。然而,在将底部添补胶层压到凸块晶片上时,必须利用精确的真空层压参数。填满凸块和芯片表面形成的台阶非常主要,由于未层压区域可能会导致全体芯片区域涌现分层征象。
随着芯片尺寸不断朝小型化方向发展,三维封装技能越来越主要,但三维封装技能也面临着诸多寻衅,微凸块的设计、超薄晶圆的处理便是个中的关键。选择得当的底部添补工艺尤其是选择得当的底部添补胶至关主要。由于间隙非常窄、凸块间距风雅,流动式底部添补工艺和材料可能无法适用于三维封装技能。因此,将晶圆级底部添补工艺、非流动式底部添补工艺和热压键合工艺相结合,成为 1 个空想的选择。晶圆级底部添补工艺中的底部添补胶是通过旋涂(针对液体型)或层压(针对薄膜型)工艺直接应用于晶圆的底部。与其他底部添补工艺比较,利用晶圆级底部添补工艺可显著缩短处理韶光,因此,该工艺已成为实现三维封装中底部添补的紧张选择。REBIBIS 等通过优化封装设计、材料选择和封装后的可靠性测试,实现了用晶圆级底部添补工艺添补具有非常窄的间隙(<15μm)、非常风雅的微凸块间距(<40μm)的器件。
五、底部添补工艺的先容
1、对添补材料的哀求
根据添补材料的特性,我们会对底部添补工艺有以下哀求:
(1)流动性要好,同时有比较好的润湿能力,能够适应的间隙,在流动过程中不随意马虎产生气泡,有较好的形 成圆角的能力。
(2)固化条件能够和现有的生产工艺流程相匹配。较长的固化韶光可能会成为生产线的瓶颈。
(3)良好的可靠性,譬如,·较高的玻化温度(Tg),与组件相匹配的热膨胀系数(CTE)等。
(4)与助焊剂有良好的兼容性。有时由于材料选择不当,助焊剂和添补材料之间会产生交互反应,使产品可靠性 迅速降落。
(5)组装完成后,组件能够承受永劫光的老化,并且暴露在湿汽中功能和可靠性不受影响。
(6)组件可以通过无铅湿敏度测试(JEDEC,Level 3)。
而在实际运用中,我们该如何选择底部添补材料呢?添补材料的选择是与产品特点干系的,每每须要在工艺和可 靠性间平衡。以下是我们在选择材料时考虑的成分:
(1)基板材料的不同,硬质板和柔性板哀求底部添补材料热膨胀系数会不一样。
(2)晶片尺寸的大小及离板的间隙会影响胶水在底部流动的速率,较大的元件须要流动速率较快的添补材料,要 考虑添补材料的流动速率是否成为瓶颈。
(3)添补材料在小的间隙中是否具有合理的流动速率。一样平常材料都会界定的添补间隙,在选择时须要考虑产 品的间隙是否知足哀求。
(4)添补材料在小的间隙中流动是否会随意马虎产生气泡,气泡的存在会降落产品的可靠性。
(5)底部添补材料对高下两侧材料的润湿力是否附近,如果差异太大,会造成流动不完全,或产生气泡。
(6)添补材料自动形成圆角的能力要强,其对元件基材具有良好的润湿能力,一部分添补材料要能够自动爬至元件 的四个侧面形成圆角。
一些底部添补材料的特性如下表1所示:
边缘圆角对付组件可靠性非常关键,它与环境、填料本身的特性、助焊剂及阻焊膜和基板的厚度干系。边缘圆角厚度是指元件下表面一边与填料由于爬升至元件侧面形成弧线的切线之间的间隔,如下图所示。
那么圆角厚度多少才得当呢?3~10 mil对一些在热循环中有较好表现的材料比较适宜。太薄则随意马虎与晶片和基 板分离,过厚则在角落出随意马虎涌现裂纹,或在附近焊点涌现分层。由于胶水分配工艺稳定性的缘故原由,胶水量在10 %内变动属于正常。如下图所示:
2、底部添补施胶前异物掌握
底部添补胶施胶前需确认板面和添补面无异物及大量助焊剂残留,较多的助焊剂残留会导致胶黏剂附着在助焊剂残留物上,后续利用过程中助焊剂残留物的挥发、软化、变异都直接影响胶黏剂机器性能,进而影响产品可靠性。标准的底部添补施胶工艺哀求先将PCBA洗濯干净并烘干,再点胶固化。
3、底部添补工艺掌握
基板在底部添补之前须要烘烤,倒装晶片基材是硅,无须烘烤。烘烤目的是为了驱除基板/组件内的水汽,防 止在固化过程中受热蒸发进入填料而形成气泡。基板/组件需储存在干燥环境中,仅在底部添补前烘烤。烘烤时 间依赖于组件/基板的布局,阻焊膜内的水汽一样平常125℃下30 min便可驱除,但内层水汽纵然125℃烘烤2h还不能 驱除。焊盘表面处理办法是OSP的基板须要考虑在烘烤过程中氧化的问题。
一样平常添补材料在一定温度下毛细流动速率较低温下快,以是底部添补材料都须要预热到一定温度,以便其在元 件底部的流动。板上预热温度可以掌握在90℃旁边,或依照材料的利用解释设置适当的预热温度。胶水一样平常保存 在-40~-60℃的低温环境中,利用前须要将其从超低温冰箱中取出回温到室内温度。胶量的掌握对付得当的边 缘圆角形成非常关键。我们可以设定如图6所示的模型,进行理论胶量的打算,但是更主要的是掌握稳定的胶水 流量,形成满意的边缘圆角。
模型建立:总的胶量可以分割成元件底部和四周圆角两
·Vt:理论胶量:
·vs:元件底部胶量:
·Vf:元件四周圆角胶量:
·I:元件宽:
·W:元件长:
·h:元件厚;
·s:元件离板间隙:
·r:边缘圆角在基板上的宽。
·n:焊球的数量
则
添补材料流动速率或添补的韶光除了与其特性干系外,还于晶片尺寸大小,离板间隙以及添补材料对元件和基 板的润湿力干系。如果晶片尺寸较大而且离板间隙小,则添补完全须要的韶光就长。添补材料对元件和基板的润 湿力差异太大,也会造成添补韶光过长,而且可能会产生气泡。填料在元件底部流动的速率还与点胶的路径有关 系,在填料流动方向上阻碍多,如焊点和阻焊膜窗口等,会造成流动速率慢而且随意马虎产生气泡。如下图所示:
好的点胶路径的安排可以得到非常好的流动效果,而且能降落填估中的气泡。如下图所示,路径1(I型)和 路径2(L型)比较常用,应只管即便避免利用路径3(U型),由于这种方框型的路径很随意马虎将元件底部的空气封入填估中。纵然选择路径1或2,也须要仔细优化画 线的是非和粗细。当画线太永劫,会导致两侧部分流动快,而中间部分流动慢,将空气封入填估中。这时推 荐利用较短的粗线,在流动方向上让填估中央部分流动稍快,避免产生气泡。但此时须要考虑倒装晶片四周是否 有足够的点胶空间,可不可以避过靠得很近的其他元件。对付周围没有太多空间的情形,有时可以在同—边同一 位置画多道细线来办理。
单路径有利于减少流动过程中卷入的气泡,但是完成添补的时问会长。如果焊盘处在阻焊膜长的窗口中,这时 应避免填料流动的方向与阻焊膜窗口的长度方向平行,由于在这种情形下,在填料流动过程中气泡很随意马虎在阻焊 膜窗口内形成,如下图所示:
填料的固化可以在回流炉或自动掌握的烤箱中完成,须要掌握加热的温度和韶光。不同的底部添补材料须要的 加热温度和韶光会不一样,温度比所哀求的低或赶过10'C会对可靠性产生非常显著的影响。温度太低,填料不 能完备固化;温度太高,则会带来氧化的问题。加热韶光的偏差该当掌握在所哀求加热韶光的⒛%以内,如果⒛ mln的圃化韶光,16 min会太短,24 min则会太长。对付一些稠浊装置,产品上可能有一些热敏元件,永劫光的 高温加热会对其造成侵害,这时工艺安排上须要考虑前辈行底部添补,然后圃化,再装置那些热敏元件。可能一 些基板焊盘是采取OSP的表面处理办法,多次受热会导致焊盘氧化可焊性降落,如果固化之后还有其他SMT工艺, 则会产生相称大的影响,在氮气中完成固化是有效的办理方案。
4、底部添补工艺的优点
(1)提高焊点的可靠性,延长产品的利用寿命;
(2)保护焊点免受环境的侵蚀,提高产品的抗堕落性;
(3)降落芯片和基板之间的热应力,提高产品的抗热循环性;
(4)增强芯片和基板之间的粘协力,提高产品的抗冲击性和抗振动性。
5、底部添补工艺的缺陷
(1)增加封装的本钱和繁芜度,须要额外的设备和材料;
(2)须要选择得当的底部添补材料和参数,以匹配芯片和基板的特性,避免产生残余应力、裂纹、堕落、空洞等失落效模式;
(3)难以对封装进行修理或重工,须要拆除底部添补物才能进行焊点的检讨或改换;
(4)可能影响芯片的电性能,如旗子暗记延迟、串扰、噪声等。
六、底部添补工艺面临的寻衅
随着倒装芯片技能的发展,无铅焊料的利用给底部添补工艺带来了新的寻衅[。无铅焊料的熔点相对较高,在高温回流过程中会因材料退化、湿气侵入和机器膨胀程度的增加而导致元件破坏。因此,须要提高底部添补胶的热稳定性,提高其对各种界面的附着力、黏接强度和断裂韧性。
对付流动式底部添补工艺,助焊剂的残留、底部添补胶之间的相容性差可能导致空隙形成。ANDRE等的研究结果表明,洗濯或加热助焊剂有助于提高界面的黏附力,因此须要开拓免洗濯的助焊剂或有效的助焊剂洗濯工艺。细间距、窄间隙芯片的发展也为流动式底部添补工艺带来了寻衅,个中涉及添补问题和助焊剂残留问题。KATOH 等开拓了无助焊剂的窄间隙添补工艺,实现了对凸块金属表面的无助焊剂键合,提高了焊料的润湿性,实现了最小间距为 10 μm的底部添补。汤姝莉等比拟不同洗濯参数和洗濯工艺的效果,提出利用真空汽相洗濯技能可以得到良好的底部添补效果。对付底部添补胶的流动、空洞的形成、其与凸块间距之间的关系等均是当前研究的重点,NG 等利用公式进行剖析建模,研究空洞形成的机理,为理解空洞毛病的根本缘故原由供应了主要启迪,并为办理该问题供应了可能的办理方案。随着打算机技能的发展和卷积神经网络模型的运用,深度学习和大数据剖析可以根据添补参数和阵列模式来预测空隙区域的形成,对添补压力、点胶模式和球栅阵列之间的关系供应定量见地,有助于人们理解倒装芯片中空洞的形成机制,从而调度设计和工艺以优化底部添补特定区域的空洞,进一步提高封装的可靠性。LING等利用卷积神经网络模型演习空洞图像,利用新图像测试模型,并利用点胶参数剖析空洞面积及其分布区域,得到了较好的实验结果。
GUO 等制备了表面改性的 nm 级二氧化硅,并将其作为添加料均匀地添加到环氧基体中,改进了底部添补胶的热机器性能和光学传输性能。由于分散程度、分散相与分散介质之间的相互浸染以及颗粒之间的相互浸染都会影响材料的性能,因此如何实现添加料的均匀分散成为将纳米复合股料运用于底部添补的关键成分。ZHU 等制备出不同尺寸的 nm 级二氧化硅,通过研发出得当的底部添补胶配方、优化底部添补工艺及构建失落效模型等方法来应对寻衅。WANG等根据底部添补胶基质选择具有得当尺寸的 nm 级二氧化硅并改进其分散性,该团队系统研究了底部添补胶的配方以优化其性能,改进了底部添补胶的动态热机器性能和热膨胀稳定性。
芯片堆叠技能已经发展到三维封装阶段,局部功率密度达到 100 W/cm2 以上,高集成芯片的散热问题尤为突出,因此底部添补胶的导热性已成为关键成分。在底部添补胶中添加具有高导热性的无机添加料,可以增强底部添补胶的导热性,进而提高芯片的可靠性。能够同时知足底部添补胶在热、电、机器、CTE、黏度等方面的性能需求非常困难,因此如何制备出具有增强导热性能的聚合物复合股料越来越受到学术界和工业界的关注。WEN 等总结了最新的研究进展,提出结合运用仿照方法以及选择得当的配方和添加料,可以知足底部添补胶在实际运用中的性能哀求,同时还应努力降落生产本钱,以实现高导热底部添补胶的规模化生产。
总结一下
底部添补工艺可以有效提高封装可靠性。目前常见的底部添补工艺紧张有流动式、非流动式、模压式和晶圆级底部添补工艺等。流动式底部添补工艺借助毛细管力实现添补,其运用广泛但添补效率较低,研究者们通过优化凸块设计,并利用超声、真空赞助等技能,以及选择得当的底部添补胶来改进添补效果。非流动式底部添补工艺可以提高添补效率,但对材料和工艺的哀求较高,须要重点办理添补后的空洞和芯片分裂问题。模压式底部添补工艺通过利用改性的EMC,将底部添补和塑封工艺相结合,从而缩短了工艺韶光;但该工艺对模具哀求高,且适用范围较窄。晶圆级底部添补工艺既可以与 SMT 兼容,又可以与非流动式底部添补工艺、热压键合工艺结合,适用于具有窄间隙、细间距的特点和三维封装的运用处景。
现阶段底部添补工艺依然面临很多寻衅。市场对底部添补胶的稳定性、流动性、黏接强度以及导热性的哀求越来越高。优化底部添补胶的配方和性能、调度添补工艺、结合封装设计以减少空洞等方法可以有效提高可靠性。利用人工智能和深度学习等新兴技能,有助于添补材料的设计、封装构造和工艺参数的优化,可以为办理潜在的寻衅供应快捷的工具。
-----End-----
免责声明:我们尊重原创,也看重分享;笔墨、图片版权归原作者所有。转载目的在于分享更多信息,不代表本号态度,如有陵犯您的权柄请及时联系,我们将第一韶光删除,感激!