作为在制造行业,日常事情每天都可能碰着不良问题,不良问题办理可以参考以下办法进行剖析和改进事情。
一、基本哀求:
1.1 基本原则:同一批次有多种不良类型时,必须
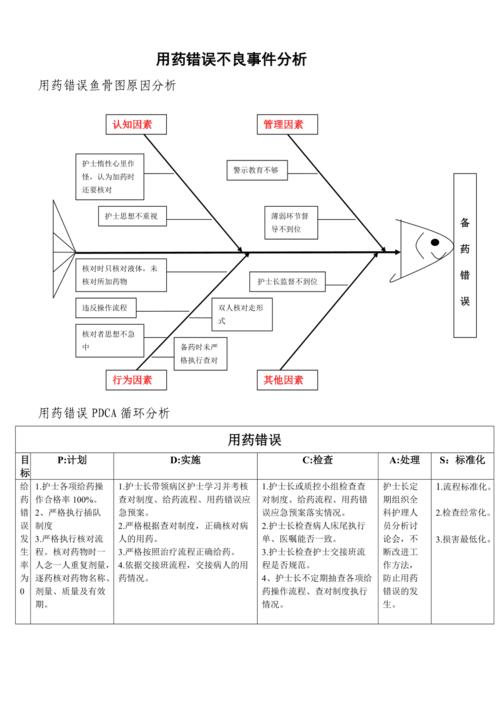
针对每种不良类型单独报告;
1.2 报告格式:客户有哀求时利用客户格式(如
8D、五原则报告、不良联结回答书等),或
利用供应商格式,但务必要覆盖干系要素要
求。必要时可添加顾客/本公司LOGO;
1.3 报告名称:如“不良调查剖析报告”等;
1.4 报告发送工具:明确要发送给的公司名称/
部门名称/职员姓名、职位等;利用敬语;
1.5 拟定审批:体例/审核/批准人职位、具名、
日期;必须由品质最高卖力人批准;
1.6 提交期限:必须在顾客哀求期限条件交。紧急
时可利用“第一报”、“第N报”、“终极报”形式;
1.7 报告编号:统一编号,建立目录,以便于存
档、查找等;
二、不良描述:
2.1 不良发生韶光;
2.2 不良发生地点;
2.3 不良创造过程简述(谁,什么工序,若何发
现,总数/批次中多少个,不良状态照片);
2.4 车型/零件号/版本(主要!
不同版本零件状态
不一样,并必须注明客户零件号,必要时注明
不良品所属总成件的零件号。)
三、现状调查:
3.1 不良征象确认(要图示,如再实际验)。根据
现场或对回收现品的调查剖析,明确不良的部
位、状态等。破损/失落效的照片(与良品对
照)、示意图等韶光、本钱许可的条件下,
可仿照不良发生的工况、作业方法等,设计
系列试验,利用良品再现不良发生的外界条
件;
3.2 确定追溯范围(批次,以及所有可能流出的环
节,从不良零件制造过程至客户端整车)不良
品的质料/制造批次,确定需追溯的范围;
3.3 针对每个追溯环节的筛查/选别结果;.
四、纠正方法:
4.1 手工对应、紧急生产等良品更换操持,担保不
影响公司内部及客户端正常生产操持;
4.2 全数选别、第一韶光良品更换、加严的检测措
施,不良品隔离、处置(返工、返修、报
废等等);
4.3 出货100%全检操持(永久对策履行前必须,
需记录并统计);
五、不良流程剖析:
5.1 按过程流程图,对所有储存、搬运、制造、装
配、考验等过程进行剖析,识别出所有可能发
生或流出的过程/工序;
5.2 针对上述每个识别出的过程/工序,是否所有
潜在失落效模式均在PFMEA中已被识别?
5.3 各失落效模式在掌握操持、作业/检讨辅导书等
有无管控,是否同等?
5.4 现场操作与规定是否同等?
5.5 是否有新人/未经培训员工作业?现有员工
节制程度?
5.6 先期过程能力剖析结果(PPK/CPK);
5.7 CP中定义的丈量/检测装置精度是否足够?
MSA履行情形?
5.8 检讨台光芒是否充足?现场储存、周转布
局/过程是否可能导致混料、异品?有无数
量管理(针对欠品)?
5.9 有无防错方法?
5.10 调机品如何管控?是否隔离报废或履行特
别检讨后放行?
5.11 返工/返修品如何管控?
5.12 各工序已加工/未加工产品有无清晰标识
和隔离?
5.13 生产停息时作业台是否清理?在制品如
何处理?
六、方法履行:
6.1 针对流程剖析结果制订;
6.2 本次不良干系特性需作为主要特性表示在分外
特性清单/CP/PFMEA/WI中;
6.3 对策后需在PFMEA中更新发生频度、探测度
重新打算RPN值;
6.4 所有修正的文件(变动前版本-变动后版本,
变动部位截图比拟);
6.5 看板更新;
6.6 现场标识(库位、区域标识等)更新;
6.7 对策履行韶光;
6.8 首批交货日期;
6.9 初品标识;
七、效果验证:
7.1 初品全尺寸检测报告,需公司内部批准;
7.2 永久对策履行一段韶光内的不良发生情形
记录和统计;
7.3 是否列入年度过程审核/产品审核操持?
八、举一反三展开:
8.1 有无类似产品/工序?
8.2 如有,履行效果?
九、教诲演习:
9.1 不良调查报告清晰展示在干系事情场所,并存
档作为新人培训用。
9.2 不良跟踪统计清晰展示在干系事情场所;务必
长期跟踪(至少一年以上)。
9.3 良品/不良品在现场比拟展示,标明不良部位
指示、如何有效辨别。
9.4 类似品在现场展示,标明差异点。
十、不良跟进案例: