在经由冲裁工序后,其集流体冲裁边缘部分涌现了过长的毛刺(图示标记部分)。长毛刺有刺穿隔膜,导致电池短路使电池失落效的风险,影响电池安全性能。
a 为负极片,b 为正极片
不雅观察到锂电池极片冲裁边缘断面情形,可以看到集流体的毛刺部分长度明显长于集流体原始厚度,而且进一步不雅观察可以创造,集流体彷佛往某方向有拉伸行为,因此上、下电池材料层厚度不一致
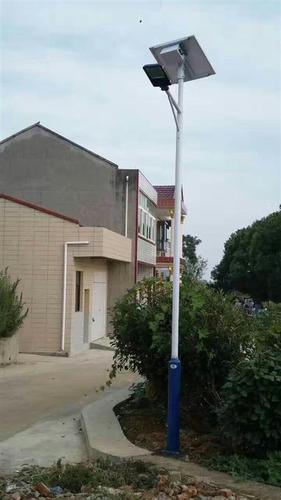
毛刺的存在对锂离子电池会造成不良的影响,要避免产生毛刺,其危害与粉尘对锂电池的危害类似,紧张分为高自放电、短路、动怒爆炸等。毛刺危害的严重程度,需根据详细位置、大小等成分综合剖断。
2.1 高自放电
高自放电是指电池在不该用的情形下,电压低落、电量损耗的征象。当这个损耗在规定的情形下超过一定量之后,这只电池就被认为是B品或报废电池。HSD很严重的时候,充满电的电池,过不了多久,电量就会损耗殆尽,乃至使电池的电压变为0V。任何情形下电压是不能低于2.0V的,如果电压低于2.0V,电池就会涌现不可逆转的化学反应,就失落去了循环充放电的能力,电池也就报废了。
毛刺造成锂电池高自放电的缘故原由是毛刺过大导致刺穿隔膜,正负极打仗引发物理短路,导致自放电加大。
2.2 短路
锂离子电池的能量,紧张由卷芯供应,个中正极片,负极是能量的源头。锂离子电池在利用时,外部电路传输电子,内部有锂离子穿梭于电解液中,在正负极材料中进行脱嵌,个中隔膜将正负极片分开。
如果毛刺过大,就会导致电池内部正极极片和负极极片直接打仗了,那电池内部就成了电子导电了,电池就会发生内部短路了。如果电池内部短路了,那么电池就大量发热,那么随着电池的大量发热,进而可能涌现动怒爆炸。
2.3 动怒爆炸
锂离子电池在满电的时候,内部溘然短路,会立即开释出大量热量,大量的热量积聚无法开释时就会致使电池迅速升温,温度升高引发电解液分解、正负极材料构造变革等,开释更多热量,产生大量气体,电池内部压力急剧上升,进而发生电池爆炸的严重后果。爆炸会使电池零部件飞溅,随意马虎伤人,也会使电解液着火,很随意马虎引发失火。极片的毛刺随意马虎使薄弱的隔膜纸刺破而导致如此重大的失落效。
毛刺的丈量早期的时候,一些企业由于资源的限定或缺少有效的标准辅导,有采纳手触或放大镜等去不雅观看丈量的。现在来看,这些丈量方法主不雅观性太强,不足科学。对付判断毛刺对电池的影响,缺少足够的依据。常日来说,肉眼可见的毛刺随意马虎识别,肉眼难以不雅观察到的毛刺一样平常达到微米级,须要更加科学的仪器来丈量,例如常用的是影像丈量仪。
毛刺的高度可以参考以下示意图,个中“B”代表毛刺,与隔膜有重合的宽度代表毛刺高度。测试毛刺尺寸则是丈量毛刺垂直方向的高度。
关键工序毛刺管控
锂离子电池极片裁切工艺紧张采取以下三种:(1)圆盘剪分切,(2)模具冲切,(3)激光切割。
4.1 极片模切(冲切)
锂离子电池极片的模切工艺又分为两种:(1)木板刀模冲切,锋利的刀刃安装在木板上,一定压力浸染下将刀刃切开极片。这种工艺模具大略,本钱低,但是冲切品质不易掌握,目前逐步被淘汰。(2)五金模具冲切,利用冲头和下刀模极小的间隙对极片进行裁切,如图所示。涂层颗粒通过粘结剂连接在一起,在冲切工艺过程中,在应力浸染下涂层颗粒之间剥离,金属箔材发生塑形应变,达到断裂强度之后产生裂纹,裂纹扩展分离,金属箔材断裂分离过程如图所示。金属材料冲切件的断面分为4个部分:塌角、剪切带、断裂带和毛刺。断面的剪切带越宽,塌角及毛刺高度越小,冲切件的断面质量也就越高。
冲切事理示意图
金属箔材冲割断裂过程
冲切工艺中上冲头和下模之间的冲切间隙,可以用如下公式(1)表示:
个中,CL为冲切间隙,D和d是高下模头的尺寸,t是板材厚度,如图所示。而考虑到模具的磨损时,有效冲切间隙Cle定义为公式(2):
个中,模具磨损过程简化为图4a所示,模具磨损量用a和b表示,当发生磨损时,随着a、b值变革,当模具发生磨损时,有效冲切间隙Cle也会相应增加,如图4b所示,有效间隙知足式(2)关系。冲切间隙和模具刃口的磨损情形对冲切过程有主要影响,随着模具的磨损,冲切间隙增加,模具刃口圆角增大,冲切件的断面质量也会发生改变。
模具磨损与有效冲切间隙 (a)模具磨损示意图,(b)有限冲切间隙随着磨损量增加曲线关系
在冲裁工序,影响毛刺大小的成分紧张有:极片的物理力学性能、极片厚度、冲裁办法、冲裁间隙、模具精度、模具材质、模具圆角、模具磨损程度等。
改进方法:优化模具构造,优化模具材料,提高模具制造与装置精度,改进模切工艺
集流体的毛刺长度随着冲裁间隙与圆角尺寸的增加而增加;
同样尺度的变革下,冲裁间隙的变革导致集流体毛刺长度的变革大于模具间隙变革所导致毛刺长度变革;
同等条件下,正极集流体的毛刺长度小于负极集流体毛刺长度;
应随时把稳模具的损耗状况,只管即便担保冲裁间隙与模具圆角至0.001mm 以下,以减少毛刺长度。
4.2 极片分切(滚剪)
圆盘分切加工过程示意图
锂电池极片圆盘剪的裁切办法的特点:
(1)极片分切时,高下圆盘刀具有后角,类似与剪刀刀刃,刃口宽度特殊小。高下圆盘刀不存在水平间隙(图1中所示参数c相称于负值),而是高下刀相互打仗并存在侧向压力。
(2)板料分切时高下基本上都有橡胶托辊,平衡高下刀在剪切时产生的剪力和剪切力矩,避免板料的大幅变形。而极片分切没有高下托辊。
(3)极片涂层是由颗粒组成的复合股料,险些没有塑性变形能力,当高下圆盘刀产生的内应力大于涂层颗粒之间的结合力,涂层产生裂痕并拓展分离。
影响毛刺的大小、断面描述特色及极片尺寸精度等质量的成分有很多,根据现有的理论,可以总结为:极片的物理力学性能、极片厚度、高下成对刀具的侧向压力(图1中参数c)、高下成对刀具的重叠量(图1中参数δ)、刃口磨损状态、咬入角(图1中参数α)、圆盘刀精度等。
(1)材料物理力学性能的影响。一样平常说,材料的塑性好,剪切时裂纹会涌现得较迟,材料被剪切的深度较大,所得断面光亮带所占的比例就大;而塑性差的材料,在同样的参数条件下,则随意马虎发生断裂,断面的撕裂带所占的比例就会偏大,光亮带自然也较小。
(2)高下成对刀具侧向压力(图1中参数c相称于负值)的影响。在极片的分切中,刀具侧向压力是影响分切质量的关键成分之一。剪切时,断裂面高下裂纹是否重合、剪切力的应力应变状态都与侧向压力的大小关系密切。侧向压力太小时,极片分切可能涌现朋分断面不齐整、掉料等毛病,而压力太大,刀具更随意马虎磨损,寿命更短。
(3)高下成对刀具的重叠量(图1中参数δ)的影响。重叠量的设置紧张与极片的厚度有关,合理的重叠量有利于刀具的咬合,其影响包括剪切质量的利害、毛剌的大小和刀具刃口磨损快慢等问题。
(4)咬入角(图1中参数α)的影响。圆盘分切中,咬入角是指剪切段和被剪板材中央线的夹角。咬入角增加,剪切力所产生的水平分力也会增大。如果水平分力大于极片的进料张力,板材要么打滑,要么在圆刀前拱起来而无法剪切。而咬入角减小,刀片的直径就要增大,分条机的尺寸相应的也要增大。因此如何平衡咬入角、刀片直径、板料厚度以及重叠量,必须参考实际工况而定。
在极片分切工艺中,刀具的侧向压力和重叠量是圆盘切刀部的紧张调度参数,须要根据极片的性子和厚度详细调度。以往的设备制造和工艺中,调刀每每短缺精确数值参数,而是凭借履历根据极片批次进行相应的调节。随着设备技能的进步,调刀技能也不断进步,并且数值化。目前涌现极片分切机刀具侧向压力气缸自动调节装置,极片分切时通过设定气缸压力来调节刀具侧向压力而掌握分切质量。
极片分切工艺的紧张技能难点在于处理毛刺、波浪边和掉粉。
常日哀求毛刺在12 微米以下,如下图工艺毛病形成的集流体毛刺,尺寸达到100 微米。波浪边和掉粉:下图是极片分切时存在的掉料和波浪边毛病。涌现波浪边时,极片分切和卷绕时会涌现边缘纠偏抖动,从而降落工艺精度,其余对电池终极的厚度和描述也会涌现不良影响。极片涌现掉粉会影响电池性能,正极掉粉时,电池容量减小,而负极掉粉时涌现负极无法包裹住正极的环境,随意马虎造成析锂。
4.3 激光切割
圆盘分切和模切都存在刀具磨损问题,这随意马虎引起工艺不稳定,导致极片裁切品质差,引起电池性能低落。激光切割具有生产效率高,工艺稳定性好的特点,已经在工业上运用于锂离子电池极片的裁切,其基本事理是利用高功率密度激光束照射被切割的电池极片,使极片很快被加热至很高的温度,迅速熔化、汽化、烧蚀或达到燃点而形成孔洞,随着光束在极片上的移动,孔洞连续形成宽度很窄的切缝,完成对极片的切割。
激光切割紧张问题是熔珠,粉尘问题,后续在梳理这方面管控
毛刺的掌握锂电池生产厂家应采纳设计或生产掌握等办法来预防毛刺引发的内短路。设计预防可包括在光箔上利用绝缘胶带或绝缘涂层等,或者通过风险评估显示毛刺高度不会造成内短路。
如果没有适当的设计预防方法(如胶带、涂层或FMEA剖析),每个切割点应在每班或每个生产批次至少检讨一次和丈量一次毛刺高度。丈量的毛刺高度应小于隔膜厚度公差下限的50%。在毛刺高度大于或即是隔膜公差下限的50%的情形下,文件化的工程剖析(如FMEA)应表明,毛刺高度在超过限定下不会导致内部短路。须要考虑的成分包括但不限于:涂层厚度、隔膜厚度、涂覆电极与未涂覆电极的面积、绝缘体和电綦重叠。
【逐日分享一点知识,有益点赞收藏】