工厂可日产超2万条轮胎
米其林上海工厂位于闵行经济技能开拓区,是环球出行行业领导者米其林集团在上海投资培植的专业乘用车轮胎制造加工基地,年产高等子午线轮胎700万条。
走进这家轮胎智能工厂,可以看到上万个传感器实时采集,剖析生产、质量、设备等上百种数据。通过智能物流、智能制造、智能检测等方面,米其林上海工厂实现了全流程的智能化再造,大大提升了工厂效率,基本上每四秒钟就可以产出一条轮胎。
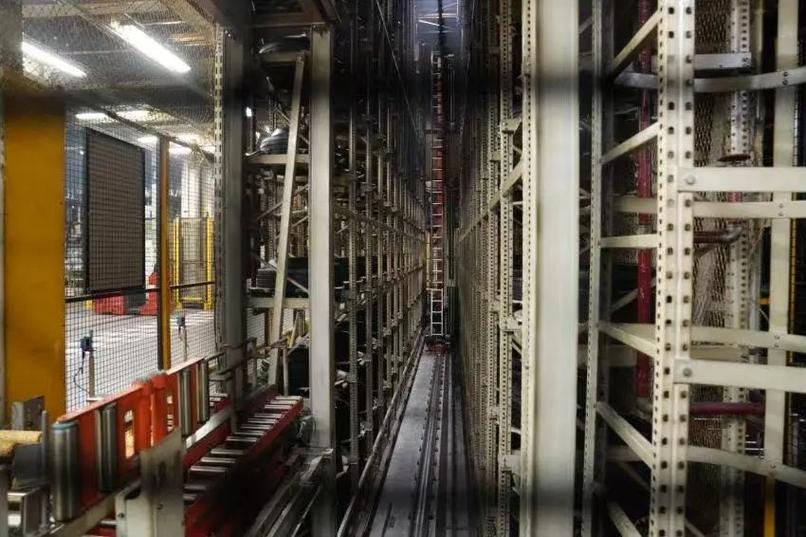
图为工人正在“标记”生胎
米其林上海工厂总经理李延冰表示:“工厂一天加起来可以生产2万到2.1万条轮胎,这个速率在以前是没有办法想象的。”
进入到未来工厂,真切感想熏染到了李厂长所说的“无法想象”——机器人码垛实现生胎到成品胎出库前全自动物流、自动扮装备配套机器人提升轮胎制造效率……除了智能物流外,智能生产和智能检测模块也在不同区域卖力事情,站在成型机旁打算了轮胎由半制品做成生胎的过程,大约在1分钟旁边,一气呵成。而按照工厂日产量打算,均匀每4秒就能产出一条胎。
“无人化”改造缩减90%人工
轮胎生产是一个别系繁杂的过程,从表面看轮胎彷佛只有一层,实在它的生产质料多达两百多种,是由多层橡胶组合而成的。准备好原材料,轮胎的生产才算正式拉开帷幕。业内人士把制作轮胎比作“蒸包子”,第一道工序便是“和面”——各种材料被运往密炼车间,即将各种材料熔合在一起。之后胶料就从密炼机内生产出来,被转运到准备车间,挤出形成胎面、胎侧、三角胶等各种半成品。紧接着,准备车间生产出的半成品部件会进入成型车间,进行下一步的合成。
成型车间是轮胎制造中最主要的工艺环节。“成型工艺尤为繁芜,内衬、胎面到胎身等几大部件的合成,都须要精准的尺寸裁切和铺放定位,确保高质量管控。”而这些步骤以往都依赖人工上料,在保持日均90%生产能力的条件下,工厂进行了设备全自动改造项目:引进了11台海内最前辈全自动轮胎一次成型设备VMI Maxx,更换了老旧低效的Krupp成型机,该设备具备视觉识别系统进行实时监控产品生产过程。项目改造后,生产效率提升很大。
不过,智能改造后对人力替代最明显的生产环节在硫化车间。“原来这个车间有200多名工人,现在只有20多个。”李厂长表示,经历成型后的轮胎虽然有了一定的形状根本,但它依然是生胎。而在硫化车间,生胎将会被“蒸熟”。“以前都是靠工人用手放进(存胎器)去的,这个车间的工人,每人每天要搬六百多条轮胎,总重近六吨。现在这个搬运事情都已经变成了自动化。”
多种机器助工人“解放体力”
在硫化车间,举头看到了帮助工人解放体力的“帮手”——一辆辆空中有轨小车,据先容,这也是海内轮胎行业首家空中EMS智能运输系统。一条条轮胎在经由全自动分拣后,由这些有轨小车运送到对应的“蒸笼”进行硫化,全体运输过程无人参与。
图为工厂智能仓储
不仅如此,硫化车间的无人化改造,也降落了工人的职业暴露。
以前在硫化车间,一位工人要管10台设备,又要搬又要放,从车间一头到另一头,从机台前面到后面,一锅接着一锅开,一锅接着一锅装。常常忙得满头大汗、精疲力尽。车间改造后,工人只须要在事情间内监测数据大屏,机器运转正常情形下,无需干预,如果机器发生非常,才须要工人大略调试,或上报工程师。
在智能工厂看到“长期主义”
采访中,李厂长也指出,智能工厂不仅是短期内的自动化提升,也是企业效益和未来代价的长期表示。
基于上海制造业的员工大多数为外地员工的背景下,劳动力获取和留用都相对有难度,随着生产效率的提高,智能化改造对工厂而言,减少了企业对劳动力获取的依赖,同时还提升了工人技能。他补充道,“去年我们工厂把工人培训作为一个改进操持,在过去两年的生产中,我们建立了不同岗位对数字化能力的哀求。”
根据李厂长的先容,因机器设备的专业性,智能化工厂各个岗位对工人对应的哀求非常详细,因此对工厂新招或现有的工人来说,数字化是一个从零到一,从无到有的过程,在这个过程中,工厂通过多种形式的培训来使工人能够达到这个哀求。
不过,他坦言,数字化对人的操作哀求实在并不高。实际上,智能改造的目的,除了提升生产效率,也是为了帮助工人生产作业的事情变得更大略。
值得关注的还有企业在数字化上所作的努力。“在制造环节人力减少的同时,我们在技能改造、产品设计、考验等方面加大了投入,我们现在更多的是须要后真个工程师、流程设计方面的工程师来把全体流程、工艺进行优化。”李厂长阐明,比如通过建立工厂数字孪生,实现智能排产、仿照优化生产流程、智能防错等,为未来工厂创造新的代价。
图文:劳动报
编辑:方佳璐