智能化在线检测技能便是通过打算机技能和自动化掌握技能,按照既定程序进行系统干系试验,通过合理判据和部分人工判断使得试验过程快速、准确地进行,从而实现系统试验过程中的快速诊断剖析和定位。
- 文章信息 -
本文引自:《智能装置工艺与装备》(作者:伸开富、程晖、骆彬)。由「智造苑」原创首发, 数字化企业经授权发布。
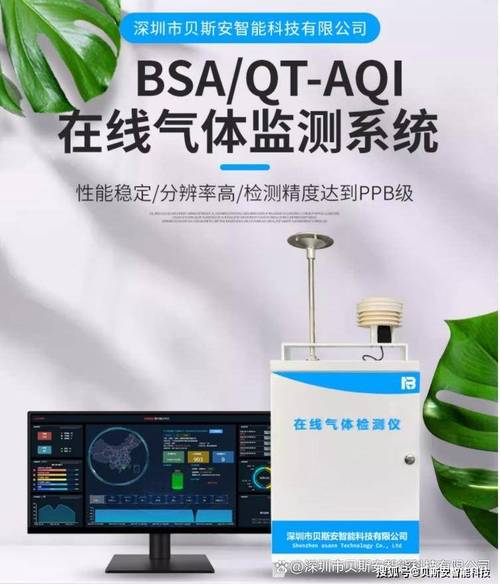
1
面向点位的
装置智能化检测技能与系统
以模线、样板、标准样件、形状卡板等为代表的传统仿照量丈量考验手段在功能、准确度和效率上已逐渐无法知足当代飞机装置丈量的需求。因此,以激光雷达为代表的高精度数字化丈量技能应运而生,在飞机装置型架定位、部件对接装置以及飞机整体装置的准确度检测中得到越来越普遍的运用,成为飞机数字化妆配关键支撑技能之一,在提高飞机制造、装置质量效率方面发挥了主要浸染。
激光雷达装置检测系统丈量事理如图1所示,利用高精度反射镜和红外激光光束丈量3个物理量:方位角、俯仰角、间隔。方位角和俯仰角是通过两个编码器实现丈量;间隔是利用调频相关激光雷达技能丈量,末了通过球形坐标系和笛卡儿坐标系的转换得出被测点的X、Y、Z坐标。
图1 激光雷达丈量事理
激光雷达丈量系统硬件由扫描头、基座、掌握柜、电源线、电脑、UPS不间断电源、打印机组成,如图2所示。
图2 激光雷达丈量硬件系统
激光雷达丈量流程如图3所示。在进行丈量时,如被测物所需数据可在同一位置得到,则将雷达放置于此处,对被测物所需数据进行丈量,丈量完成后即可对数据进行相应处理以得到被测物体所需尺寸和相对位置。若丈量物体在同一位置无法获取到所有信息时,须要用仪器丈量位置的移动来实现,即须要对仪器进行转站(转站即仪器通过丈量公共目标的位置解算求出各站仪器到统一的丈量坐标系的坐标转换参数,从而将仪器从自身坐标系下转换为统一的丈量坐标系下,实现丈量数据的统一性)。
图3 激光雷达丈量流程
iGPS丈量系统事理:该系统紧张利用三边丈量事理建立三维坐标体系来进行丈量。个中的丈量探测器根据激光发射器投射光芒的韶光特色参数,打算探测器相对付发射器的方位和俯仰角,将仿照旗子暗记转换成数字旗子暗记并发送给吸收处理器系统,采取光束法平差事理实现各发射器之间的系统标定,然后采取类似于角度空间前方交会的事理解算空间点位坐标及其他位置信息。
iGPS丈量系统构造如图4所示,紧张由激光发射器、传感器(3D智能靶镜)、吸收处理器系统软件构成。
图4 飞机数字化iGPS装置丈量系统构造
iGPS丈量的上风:
① 可以实现自由组网式和基准点建站式两种组网办法;
② 可以用于飞机数字化妆配过程中的数字化丈量;
③ 相对激光跟踪仪的比拟丈量精度可以达到0.2mm/10m。
2
面向型面的
装置智能化检测技能与系统
产品表面质量是衡量产品性能的主要指标,以飞机为例,紧张包括表面范例质量特色,如对缝间隙、阶差、钉头凸凹量、钉头与基孔间隙、蒙皮外表面波纹度等;表面质量毛病,如划伤、刻痕、压坑、变形等;蒙皮外缘技能哀求,如气动形状容差等。
利用三维表面毛病丈量系统,对被测铆钉、划痕等轮廓特色进行扫描,通过投影于被测表面条纹相位变革,获取表面密集点云数据,以此快速得到待测部位的尺寸、特色等信息,经由打算机赞助软件的打算,能够得出待测表面质量特色的详细丈量数据,实现了定量评价铆钉凸凹量、划痕深度等表面质量的目标。同时通过总结铆钉凸凹量详细算法,对数据剖析软件进行二次开拓,实现了快速定量评价铆钉凸凹量。
在装置过程中存在诸多阶差和间隙,以飞机中蒙皮对缝之间、蒙皮与构造之间、舵面与构造之间、机身部段之间、整流罩壁板之间等。阶差和间隙超过设计容限会对飞机的装置质量、翱翔性能、隐身性能等造成严重影响,因此须要对其进行精确检测。针对装置过程中间隙、阶差等表面质量特色,采取“激光间隙枪”进行装置间隙、阶差质量检测(图5),量化丈量结果,提高了产品表面质量检测水平。
图5 装置间隙、阶差检测
3
其他装置智能化检测技能与系统
除传统检测方法以外,以飞机为代表的高端装备哀求产品装置过程中对各系统进行检测,包括密封检测、整机线缆检测和机载系统检测。上述检测一贯采取传统检测手段,效率低、准确性差、劳动强度大,以是越来越多的智能化检测技能与系统得到了广泛的运用。
1)密封性检测
密封性检测紧张是考验一定几何空间内的各个连接部分是否存在泄露。由于航空航天产品服役环境的分外性,必须对相应的零件进行密封性检测。
各种密封性检测方法优缺陷比拟见表1所示。
表1 常用密封检测方法比拟
(1)超声法检测。超声波是一种高频短波旗子暗记,具有很强的方向性,这种声波是不能被人耳所直接听到的,但我们透过超声波密封性测试仪可完备侦测到这些声音。从物理学可以知道,气体总是由高气压侧流向低气压侧,当压差只涌现于小孔处时,气体产生的湍流将在小孔处产生超声波。
利用此事理,利用超声探测技能可以精确定位气体泄露点,因而可以用于对毛病点的定位。利用360°超声波旗子暗记发生器可以在容器或舱室内产生超声波旗子暗记,如果容器或舱室的密封存在毛病,超声波旗子暗记就会从毛病处泄露出来,用超声波密封性测试仪可以吸收到泄露出的超声波旗子暗记。仪器受用独特外差法将这些超声波旗子暗记转换为声频旗子暗记,让利用者透过耳机可以听到声音,并于仪器显示屏上看到强度指示,判断泄露点与泄露量的大小。外差法的事理就像收音机,可将旗子暗记准确地转换为声音,使人们随意马虎地辨认和理解。超声波技能的优点便是随意马虎理解、更加方便,其具有如下特性:
①超声波具有方向性;
②超声波很随意马虎被阻隔或遮蔽;
③超声仪器能用于噪声环境;
④超声波的变革可预知潜在的问题;
⑤超声仪器操作更随意马虎。
以是超声波探测被广泛运用于汽车密封性检测、风噪声检测、漏水检测、飞机密封性检测、舰船密封性检测、压力容器泄露测试等中。
在航天器中有许多系统可以采取超声波仪器进行检讨。一些常见的运用有测试燃油单元、氧气系统、热空气管道、机舱压力、轮胎泄露、气浮装置、液压阀和驱动装置的泄露。它同样也可用于创造驾驶室门窗泄露,只须要3个步骤就可以定位到飞机座舱密封的泄露点。
如果对大型商用飞机进行高处或远间隔检讨,合营集波器利用定位,最大定位间隔可达50m。例如压缩气体系统、阀、马达泵等,这些均可产生超声旗子暗记。一些高频声音来自于湍流,其他来自摩擦。部件开始磨损,发生故障或泄露,有着正常超声波形式的一个变革,这可作为一个增量振幅、一个音质的变革或一个音式的变革被探测。由于轻便、易用和灵巧性,超声波密封性测试仪可被用于所有航空器检测。超声波密封性测试仪可探测到瞬间的超声变革并转换此旗子暗记,以使它们可通过耳机被听到和作为强度增量在一个显示仪表面板上被不雅观察到。通过利用扫描式或是打仗式的插入模块,可以检测到设备的泄露或机器故障问题。机载录音和数据导人可帮助操作职员记录声音范例和进行精确的状态剖析。须要在本安环境中进行检测的客户,可以供应具有本安额定的定制仪器。
对付一样平常的泄露检测,在扫描模式下,沿被测试区进行轻微颠簸式移动,倾听最大声的“嘶嘶”声并跟踪这个声音到最响点,须要时调度灵敏度拨号盘进行灵敏度调度。在同样办法下利用360°超声波旗子暗记发生器测试座舱压力和驾驶舱窗的泄露,对付阀门和实行器,打仗上游并降落灵敏度到中线读值,并与下贱的读值进行比拟。
(2)氦质谱检漏。氦质谱检漏仪是利用氦气作为示漏气体的专门用于检漏的仪器,它具有稳定性高、灵敏度高的特点,是真空检漏技能中灵敏度最高的、利用最普遍的检漏仪器。
氦质谱检漏仪是磁偏转型的质谱剖析计。单级磁偏转型仪器灵敏度为10-9~10-12Pa·m3/s,广泛地用于各种密封系统及零部件的检漏。双级串联磁偏转型仪器与单级磁偏转型仪器比较较,噪声显著减小。其灵敏度可达10-14~10-15Pa·m3/s。适用于密封哀求高的系统、零部件及元器件的检漏。逆流氦质谱检漏仪改变了常规型仪器的构造布局,被检件置于检漏仪主轴泵的前级部位,因此具有可在高压力下检漏、不用液氮及质谱室污染小等特点,适用于大漏率的检测,其灵敏度可达10-12Pa·m3/s。
以用于C919飞机油箱泄露的检测的大型客机整体油箱检漏系统为例,如图6所示。该检漏系统通过对飞机油箱整体漏率检测、对单点漏源定位,以实现飞机油箱泄露的排查。系统具有自动配气功能,可任意设定氦气、空气稠浊比例,并可自动调节压力,节约本钱,飞机油箱的总漏率与单点漏率可同时丈量,效率高;并且检测结果可溯源。
图6 飞机整体油箱气密检测设备
2)装备线缆检测
工业产品制造是一项繁芜的系统工程,尤其对付飞机制造,对付电气部分(线缆、线束等)的检测是飞机各部件、总装整机阶段必不可少的一项主要事情。电气部分检测紧张是针对的是整机线缆的导通性能和绝缘性能的检讨。机上线缆的导通、阻抗、绝缘检讨和快速故障定位是飞机总装置过程中的主要步骤,对飞机的安全性、可靠性具有非常主要的意义。
目前,海内飞机线缆导通/绝缘检讨紧张以人工测试为主,其缺陷紧张有:
①低测试效率以及低速率,一架飞机的测试要花费很永劫光。
②人工测试方法面对巨大的事情量,随意马虎导致疲倦、缺点或故障,不能形成一个完全的体系,且无法追溯质量测试报告,质量掌握手段掉队。
③人工测试仅能检测开关/ 短路情形,不能在完全线缆网络中检测出回路破坏、短路、缺点连接以及其他故障。
④不能快速、准确判断单线对其他线或者接地的绝缘(线间绝缘)。
近年,全机线缆自动化检测手段也在逐步推广运用。对付点数相对较少(2万点以内)的中小型飞机,采取全机线缆集成检测是基于全部利用工艺转接电缆的方法,事情量和事情效率相对能够接管。
我国正在研制的大型飞机(如C919飞机等)线缆检测事情的特点:
①全机检测点数多,检测周期长。全机线缆集成检测现场支配大量的工艺转接电缆(该型机的测试点数不超过2万点),如图7所示。但对付大型飞机来说,测试点数是战斗机的2倍,测试方案如果仍旧采取传统的测试方案则是不可取的,转接电缆的存取管理和设计制造本钱以及测试准备阶段的事情量都非常巨大。据统计,4万点的转接电缆(拣选、上机、连接)至少须要3天韶光,事情量和事情效率均无法接管。
图7 全机线缆集成检测现场图
②整机检测点分布范围广且分散,检测难度大。全机检测点数分布范围遍布全体机身体和机翼,尾翼部位、发动机短舱也有覆盖。检测过程中间隔较远,易造成检测错位,如果全部采取转接电缆连接测试点的方法费时费力。
③电子设备集中放置。大型飞机因安装空间相对充裕,可以集中设置电子设备柜/设备架用以集中安装、放置打算机类的电子设备。在狭小空间内电子设备的集中放置对该区域的线缆检测带来困难。如果全部采取转接电缆的测试方案,会造成局部检测电缆数量多,极易造成电缆连接缺点和电缆的破坏,同时给工艺转接电缆安装、分解造成困难。
对付全机线缆测试,针对国产大飞机线路检测事情特点,设计研发了大型飞机全机线缆自动化检测系统,实在用于大型飞机特点的数字化、自动化检测技能,能够极大地缩短大型飞机的总装置周期,并显著提升产品质量。
3)机载系统检测
飞机机载系统用于担保翱翔安全、完成翱翔任务,是飞机的主要组成部分。飞机的机载系统包括机电系统和航电系统。
机电系统包括液压系统、燃油系统、电源系统、航空电力系统和环境掌握系统和机轮刹车系统等。航电系统(综合航空电子系统)紧张包括人机交互系统、翱翔状态传感器系统、导航系统、外部传感器系统。在飞机制造过程中航电系统的测试一样平常采取综合测试的手段。
(1)机载测试系统的发展。机载测试设备作为机载测试系统的主体,我国机载测试设备的发展至今已经经历了4个阶段:
①机器式、电磁式仪器——单路丈量阶段。20世纪50年代,用于翱翔试验的测试仪器是“翱翔自记器”。这种翱翔自记器按功能分为高度、速率、过载姿态角速率、振动、位移、操纵力等类型。因其记录的参数少,效率低,精度差,处理数据韶光长,逐渐被“光学示波器”所取代。光学示波器比自记器单独分散的纸带记录判读方便。
②磁记录——多路丈量阶段。由于从60年代起电子技能和电子测试仪器就开始进入到飞机试飞测试领域。磁记录具有自动化、精度高、速率快、可重放等优点,被广泛运用到翱翔试验中,如JCS-2D-J数据采集系统。这是一种以脉冲编码调制(PCM)办法的机载磁记录器,通道数可达256,总采样率2560次/s,紧张丈量缓变和数字参数,精度0.5%,并配有地面数据处理打算机,让试飞机载测试面貌焕然一新。
③综合测试阶段。随着科技的发展,测试设备的智能化,20世纪八九十年代,我国试飞机载测试迈进了综合测试及实时数据处理阶段。具有代表性的测试系统有:达明V和达明VI数据采集和处理系统。这是一种PCM办法的数据采集磁记录系统。数据采集采取了可编程序技能;一样平常情形下,达明V的总采样率为4KB/s,达明V的总采样率为32KB/s。达明系列的测试系统是12位编码,并且能按时序逐路采集每个参数。
④分散式测试阶段。21世纪伊始,由于试飞测试任务的须要,分散式测试系统也被运用到机载测试领域。它具有很多特点:采集数据量大;可靠性高;掩护方便;扩充随意马虎。目前实际试飞机载测试系统紧张是这种分散式测试系统。
(2)国产机载测试系统的运用。对付机电系统,大型客机液压系统、飞控系统和起落架系统测试的铁鸟可以实现飞机各系统交联试验。其余,基于半仿真和智能剖析技能的直升机燃油系统各项指标的测试方法及设备,其燃油温度丈量精度为±0.1°,燃油压力丈量精度为±0.001KPa。随着虚拟试验技能的发展,民航飞机液压系统虚拟性能样机平台,通过该平台可以在飞机试验验证阶段,可早于物理综合集成试验开展系统虚拟试验,有助于加快飞机研制过程中办理系统集成带来的技能问题的周期,丰富飞机系统功能、性能测试验证的手段。
对付航电系统,在飞机制造过程中航电系统的测试一样平常采取综合测试的手段,电鸟便是航空电子系统综合试验平台。其自主集成、培植了全新的大型客机主要航空电子系统地面仿真与测试试验环境,形成了覆盖全部航电系统的全方位系统综合试验环境和能力,其通过模型和脚本可以实现自动化测试。对付航电系统中的导航系统,针对飞机大型无线电导航识别系统的功能特性和目前紧张的检测需求,设计一套相应的自动测试系统。全体系统通过将软件和无线电综合技能进行整合,兼顾便携性,分别经由无线以及有线的路子完成对飞机无线电导航设备的基本功能以及特性的室外测试。其自动测试系统通过嵌入式系统和无线电软件相结合,能够完成实际运用层面对飞机无线电导航设备进行自动测试的任务,并在此根本上兼顾了便携式性和抗滋扰性能。
飞机机载系统的测试正逐步集成化和综合化。国产大飞机对机载系统进行三鸟联试,包括测试飞机飞控系统、液压系统和起落架系统的铁鸟、进行飞机发电和配电等供电系统测试的铜鸟和航电系统测试的电鸟。通过三鸟联试来仿照翱翔状态,试验职员便是在这些设备上对飞机的系统进行剖析、验证、调试,如图8所示。
图8 飞机三鸟联试平台