这条全新的钢筋骨架生产线,是在国铁集团的辅导下,由中国铁设、广东铁投、中铁七局、建科机器、河北工业大学以及天津新松等机构联合研发。据先容,通过“产、学、研、用”的深度领悟,团队成功办理了钢筋骨架搭建的技能难题,实现了少人化作业、高质量生产的目标。
高铁预制箱梁钢筋骨架智能建造生产线投产。
在工艺设计方面,项目团队首次提出了适用于智能建造的钢筋骨架成型方案,将单榀箱梁拆分为超大型钢筋网片、超大型钢带网、大U形钢筋及定位网片等部品,并通过了路内专业专家评审。
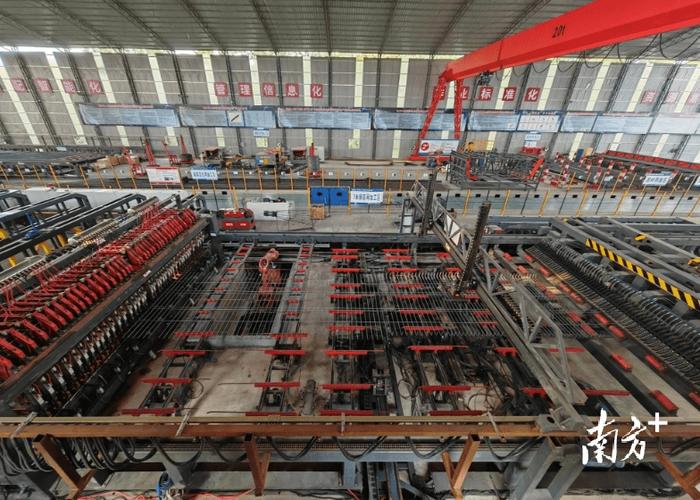
“大略来说,便是预制箱梁钢筋绑扎由人工绑扎变为线式组合,实现部品化加工、自动化拼装,机器化换人、自动化减人。”中铁七局茂名制梁场总工程师齐亚北阐明,就像搭积木一样,传统的便是人工一根根钢筋抬到指定位置,并进行绑扎;现在将钢筋骨架分解为多个适用于自动化加工的钢筋网片,分解之后的网片可利用新研设备进行自动化加工,并采取“拼装式搭建”的办法,完成主体钢筋的整体拼装成型。“通过自动化生产,钢筋之间的间隔会更平均,实现精确化建造。”齐亚北说。
钢筋网加工区。
在部品加工装置生产线方面,项目团队研发了超大型钢筋网焊接机、超大型钢带网焊接机、U形钢筋波折中央及自动排料装置、预应力孔道定位网焊接机以及装置化组装生产线。这些设备具有高度的自动化和智能化特性,大大提高了生产效率和质量。
以超大型钢筋网自动焊接机为例,它能完成最大32m×10m平分歧规格的钢筋网片制造,集矫直、运送、落料、焊接和弯钩于一体。通过高质量、自动化的电阻焊接技能,实现了网片加工的高精度掌握,达到了成品质量标准。生产过程只需一人操作一人赞助,大大减少了人力需求。
U形钢筋波折中央及自动排料装置则通过自动化技能,实现了钢筋原材的自动计数上料、自动定尺剪切、自动抓取、自动落料定位以及箱梁U形钢筋一次自动波折成形等操作。这不仅提高了生产效率,还避免了人工操作可能涌现的偏差。
钢带网加工区。
在智能掌握方面,项目团队研发了简支箱梁钢筋骨架全过程生产实行系统(MES),实现了算法智能化排产、远程信息化做事、多方位数据自动采集等功能。基于风雅化管理,他们还取消了大型钢筋部品的暂存区,避免了部品的重复起吊,全面提升了现场管理水平。
中铁七局广湛八标干系卖力人认为,这是一项具有重大意义的创新,标志着中国高铁培植向着数字化、智能化方向迈出了坚实的一步,它不仅将提升中国高铁的培植效率和质量,还将为环球高铁培植供应新的思路和方向。
南方+ 邹祥亮
通讯员 武聚盟
【作者】 邹祥亮
【来源】 南方报业传媒集团南方+客户端